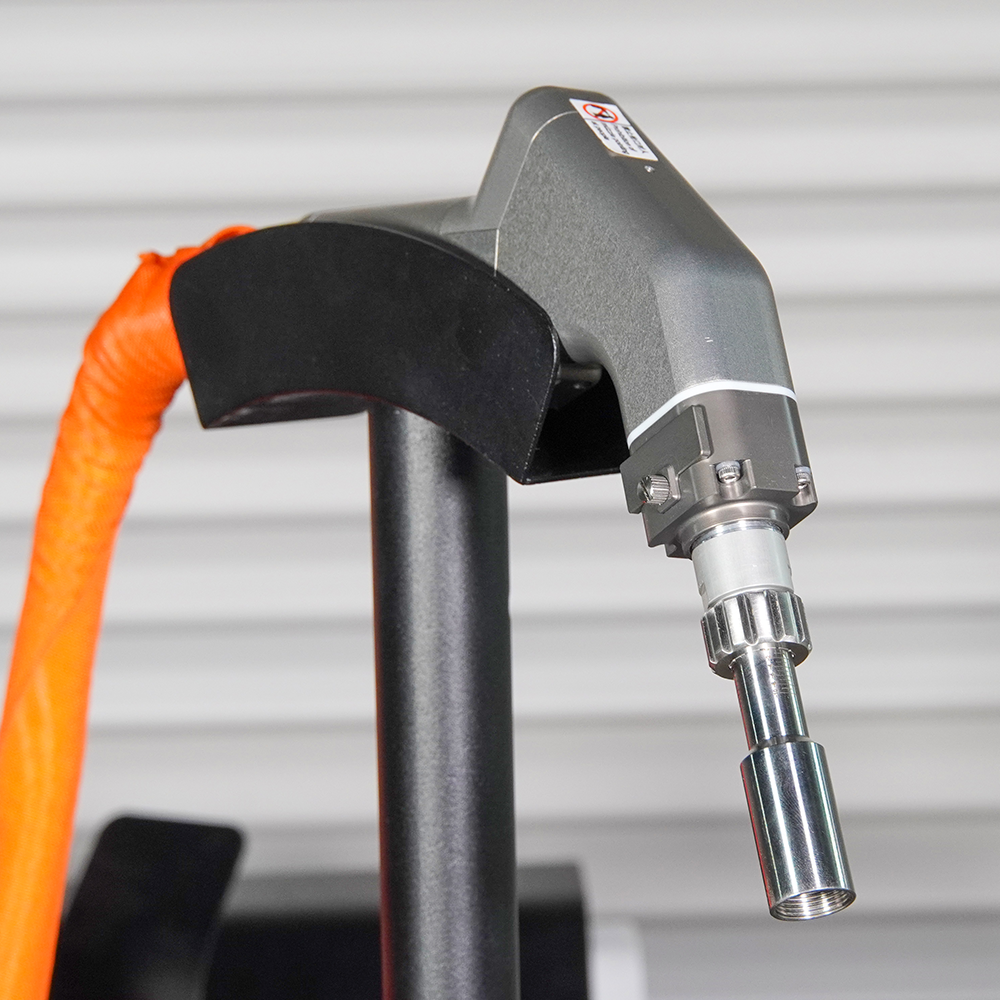
The Rise of Handheld Laser Welding in Metal Manufacturing
Handheld laser welding has emerged as a game-changer in the metal manufacturing industry, offering unparalleled precision, speed, and versatility. As we move into 2024, this cutting-edge technology is poised to transform the way metal fabricators approach their craft, delivering superior results while streamlining processes and reducing costs.In this article, we’ll explore the current status of handheld laser welding in metal manufacturing, delving into the key factors driving its adoption and the advantages it offers over traditional welding methods. We’ll also take a closer look at the latest advancements in handheld laser welding technology and how they are shaping the future of the industry.
The Advantages of Handheld Laser Welding
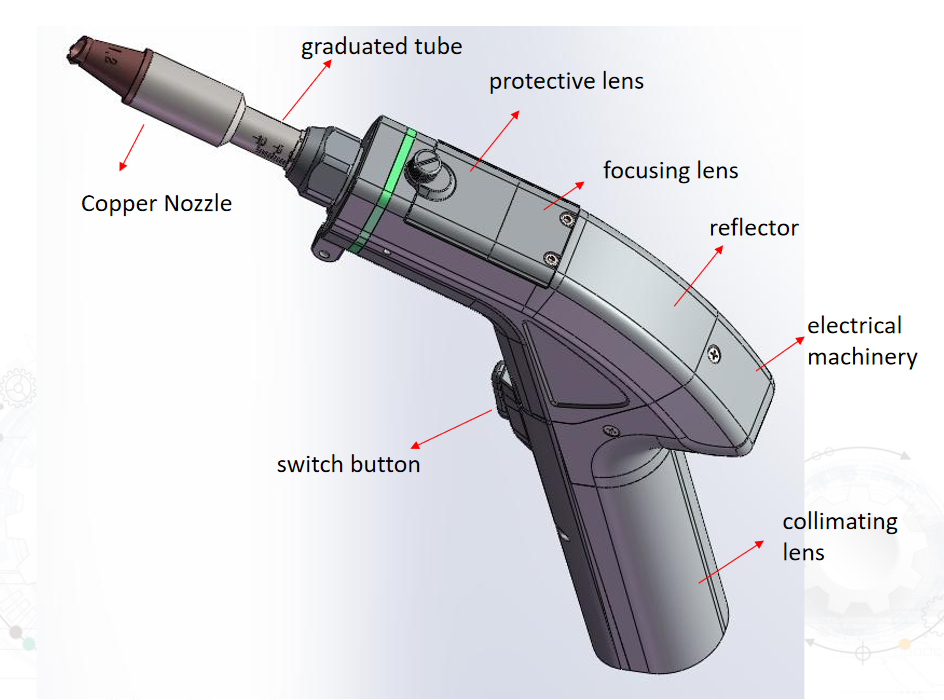
Handheld laser welding offers a host of advantages over traditional welding methods, making it an increasingly attractive choice for metal fabricators:
- Precision: Laser welding allows for precise control over the heat input, resulting in narrow, high-quality welds with minimal distortion or thermal damage to the surrounding area.
- Speed: Handheld laser welding can be up to four times faster than MIG welding, significantly increasing productivity and reducing labor costs.
- Versatility: Laser welding can be used to weld a wide range of materials, including aluminum, copper, and even dissimilar metals, making it suitable for a variety of applications.
- Automation: Handheld laser welding can be easily integrated into manufacturing workflows, allowing for increased productivity and improved consistency in the final welded product.
- Reduced Heat Input: The focused energy of a laser beam results in a smaller heat-affected zone, minimizing distortion and thermal damage to the surrounding material.
- Improved Safety: Laser welding generates less smoke and fumes compared to traditional welding methods, reducing the risk of exposure to harmful substances for welders.
- Increased Strength: Laser welding can produce welds that are as strong, or even stronger, than those created by traditional welding methods, depending on the materials and joint design used.
- Reduced Post-Processing: The precision of laser welding often eliminates the need for post-processing steps like grinding, reducing labor costs and improving efficiency.
- Portability: Advancements in laser technology have made handheld laser welding machines more compact and portable, allowing for greater flexibility in workspace setup.
- Cost-Effectiveness: As laser technology continues to advance, the cost of handheld laser welding systems has become more accessible to a wider range of metal fabricators.
The Future of Handheld Laser Welding
As the metal manufacturing industry continues to evolve, handheld laser welding is poised to play an increasingly important role. The technology is expected to see further advancements in areas such as:
- Increased Power and Speed: Laser welding machines are expected to offer higher power output and faster operating speeds, allowing for the processing of thicker materials and increased production efficiency.
- Improved Automation and Intelligence: Advancements in electronic technology, automatic control technology, sensor detection, and information processing are driving laser welding towards higher efficiency, increased automation, and enhanced intelligence.
- Multi-Wavelength Laser Systems: The development of multi-wavelength laser systems will extend the applicability of laser welding to a broader range of materials, including those traditionally difficult to weld.
- Integration with 3D Printing: The convergence of 3D printing technology and laser welding promises to create entirely new production methods capable of creating more complex and lightweight parts and assemblies.
- Micron and Nano-Scale Applications: As industries continue to miniaturize, the need for micron- and nanoscale welding will grow, potentially leading to advancements in laser welding at these scales to meet the needs of industries such as electronics, optics, and medical devices.
The Impact of Handheld Laser Welding on Metal Fabrication
The adoption of handheld laser welding is already having a significant impact on the metal fabrication industry, with many top metal fabricators embracing the technology to stay competitive and meet the demands of a rapidly evolving market.One of the key advantages of handheld laser welding is its ability to handle specialized materials with precision, such as aluminum alloys, brass, and copper. This empowers metal fabricators to venture into upscale markets and craft components tailored to precise requirements, serving industries like semiconductors and defense.Moreover, the speed and efficiency of handheld laser welding allow metal fabricators to handle more orders in less time, effortlessly meeting the surging market demands. The technology’s adaptability also enables metal fabricators to broaden their business horizons, catering to diverse customer needs, from crafting small parts to assembling large structures.
Conclusion
As the metal manufacturing industry continues to evolve, handheld laser welding is poised to play a crucial role in shaping its future. With its unparalleled precision, speed, and versatility, this cutting-edge technology is revolutionizing the way metal fabricators approach their craft, delivering superior results while streamlining processes and reducing costs.As advancements in laser technology continue to drive down costs and improve performance, handheld laser welding is becoming increasingly accessible to a wider range of metal fabricators. By embracing this transformative technology, metal fabricators can stay competitive in an intensely competitive industry and position themselves for success in the years to come.