Basic component
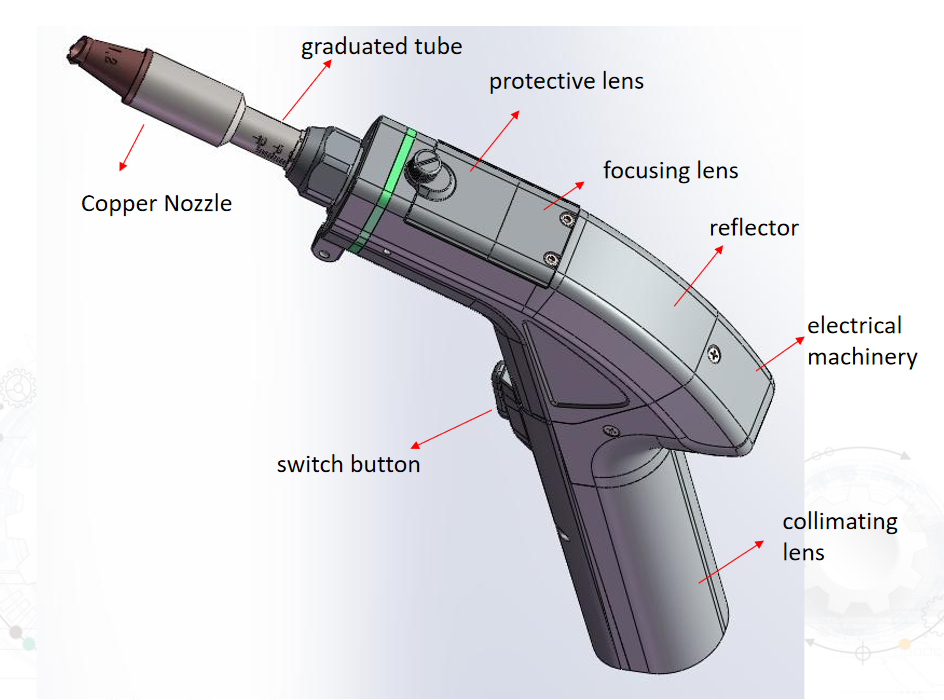
QBH’s connection
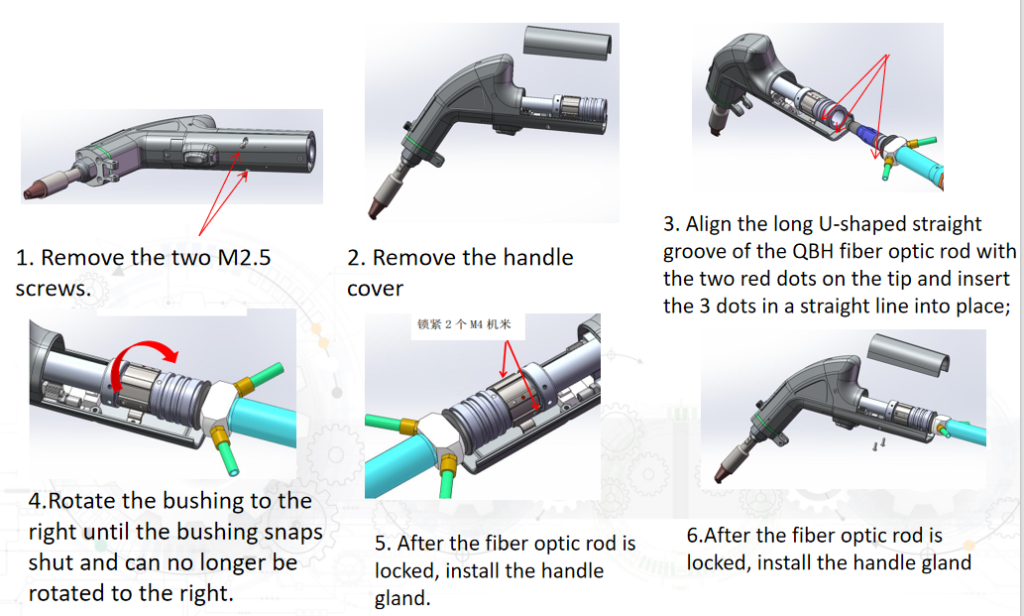
1.Current model: Displays the currently connected laser device model.
2. Switch control:
2.1 Laser Enable: Open – Allow laser output, prerequisites for light emission (laser emission steps: ① Turn on the laser
Light enable->②Safety lock conduction->③Align the workpiece and press the trigger)
2.2 Galvanometer enable: turn on/off the galvanometer;
2.3 Wire feed enable: On – the wire feed enable output is automatically triggered after the laser emits light;
2.4 Burst Enable: Open – The laser light emission mode changes from continuous light emission to intermittent light emission (pulse type) according to the burst parameters.
Off – the laser light emission mode changes from intermittent light emission (pulse type) to continuous light emission
3.Current process: 1) CS = material type – carbon steel (SS = stainless steel, AL = aluminum, GS = galvanized sheet, Other = other metals) 0.5mm = material thickness
4. Current parameters: Displays the parameters of the current process. The parameters on this page can only be used for display and cannot be used for modification. To perform modifications, please switch to the process page.
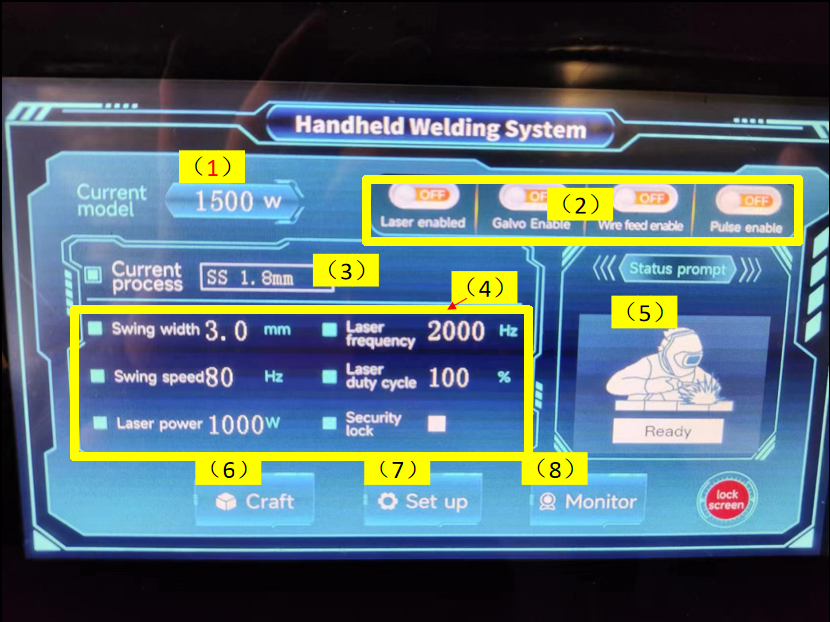
5.Craft button
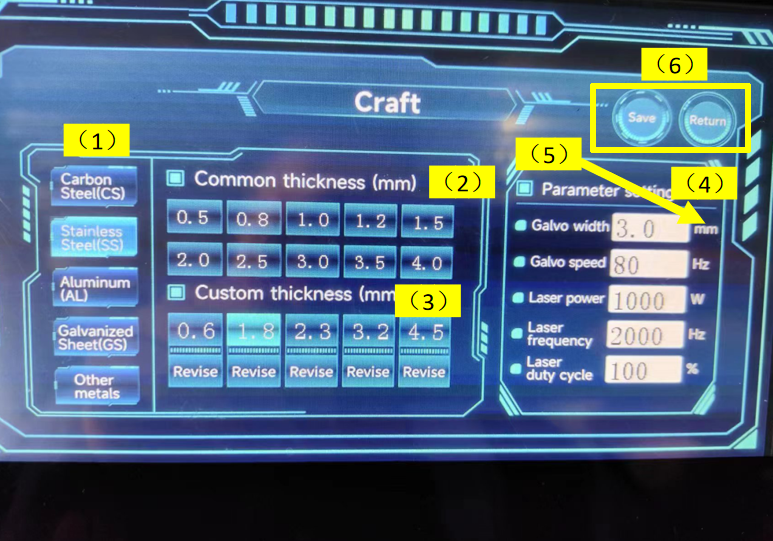
Parameter settings
1.1 Width threshold: The factory-configured copper nozzle is only allowed to be set to a maximum of 4.0mm. If you want to set a width value greater than 4mm, please replace the large-diameter copper nozzle first.
1.2 Width correction: Value range: -100~100, the value means to expand the current swing width by a percentage, a negative value means to reduce the current swing width by a percentage;
1.3 Center correction: Value range: -10.0~10.0, decrease to move to the left, increase to move to the right, applied to adjust the axis red light center;
1.4 Slow-rising time: value range: 0~3000, determined by the process power during lighting
N1 percent, progressively to 100%
1.5 Slow-rising power: value range: 0~100,
1.6 Slow down time: from 100% of the process power when turning off the light,
Progression to N2;
1.7 Slow power reduction: value range: 0~100
1.8 Gas opening delay: Value range: 0~3000, press the trigger, continue to release gas first, and then emit light. Reasonably setting the switch gas delay can well protect the molten pool from oxidation and prevent slag return from damaging the lens.
1.9 Gas-off delay: Value range: 0~3000. The actual effect is to release the trigger. After the laser stops emitting light, it will continue to emit gas and then stop emitting gas. Reasonably setting the gas-on and off delay can well protect the molten pool from oxidation and prevent Return slag damages lenses
1.10 Number of burst points: Value range: 0~128. According to the set burst duration and interval, the output will continue until the trigger is released or the safety lock is disconnected. If you want the fish scale effect, please open the homepage to enable burst shooting.
1.11 Burst duration: value range: 0~3000
1.12 Shot interval: Value range: 0~300
Model setting: Value range: 100~3000. The laser model is the maximum power calibrated by the laser manufacturer used. Please fill it in correctly; Language selection: Supports six languages: Simplified Chinese, Traditional Chinese, English, Korean, Russian, and Japanese. Factory reset: A pop-up window will pop up on the page, prompting whether you are sure to restore the factory; the system will automatically restore the factory default process Save/Return: Save: Save the currently modified data; Return: Jump to the page, jump to the home page;
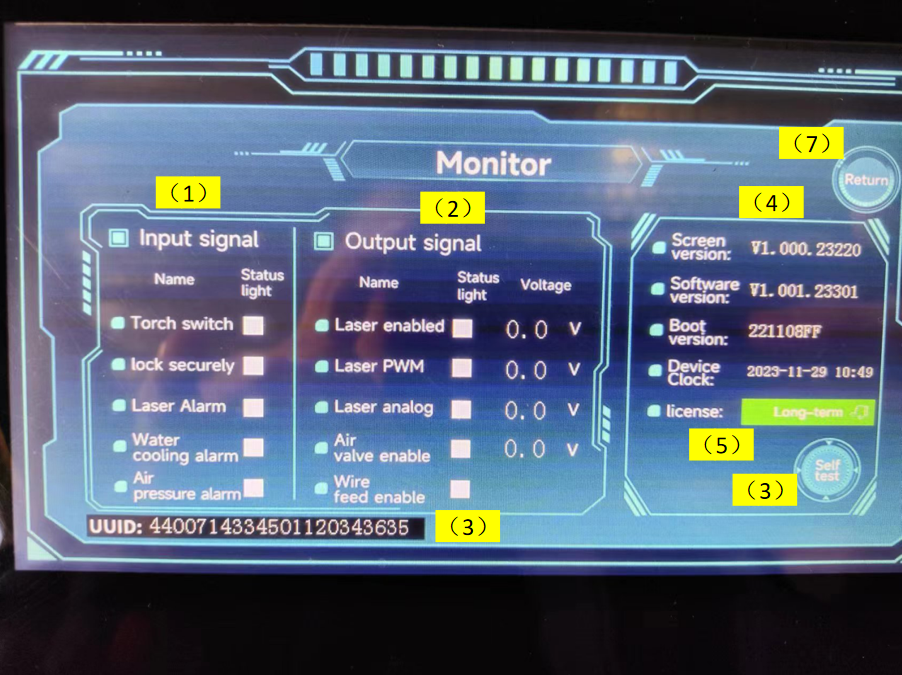
Laser cutting system
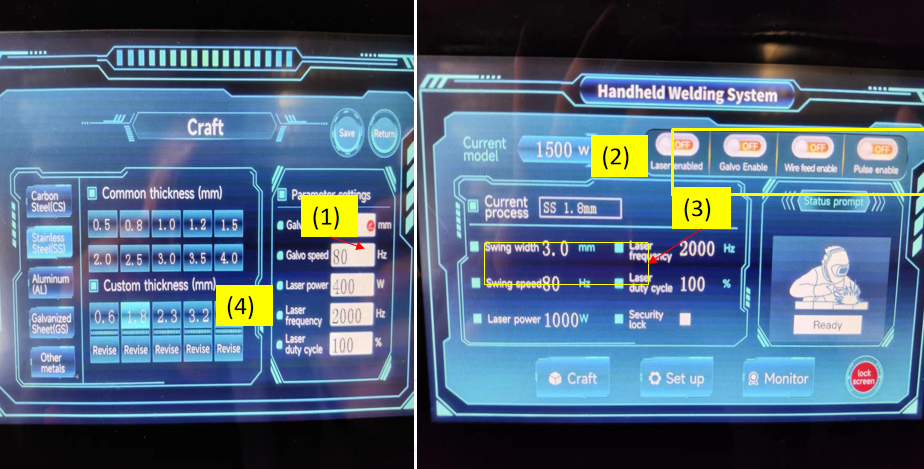
Open the process, adjust the galvanometer width (1) to zero, adjust the laser power (4) to the appropriate power, click Save and Return, the page is on the right at this time, (3) is 0 at this time, turn on the laser Enable the button to cut, adjust the appropriate power and air pressure during the cutting process, and replace the special copper nozzle for cutting.
Laser cleaning system
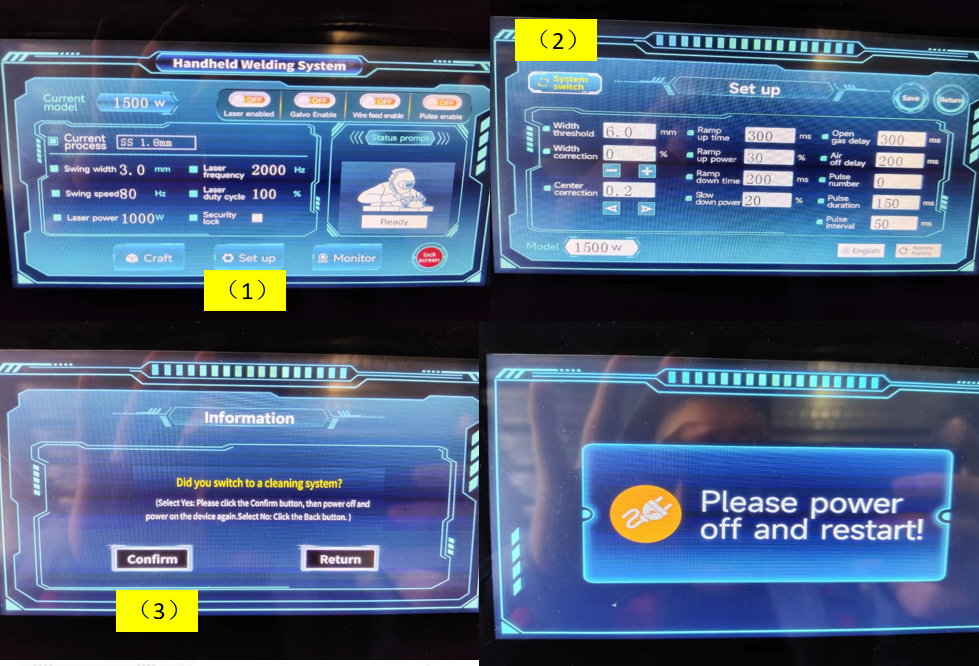
Laser cleaning system: Click Settings (1) and enter the password 666666, click System Switch (2) to confirm (3). The system will enter the power-off and restart state. After power-off and restart, it will enter the page shown below, turn on laser enable (4), vibrator Enable the mirror (5), adjust the laser power, swing frequency, and swing width (6), disassemble the welding joint scale tube, and clean it.
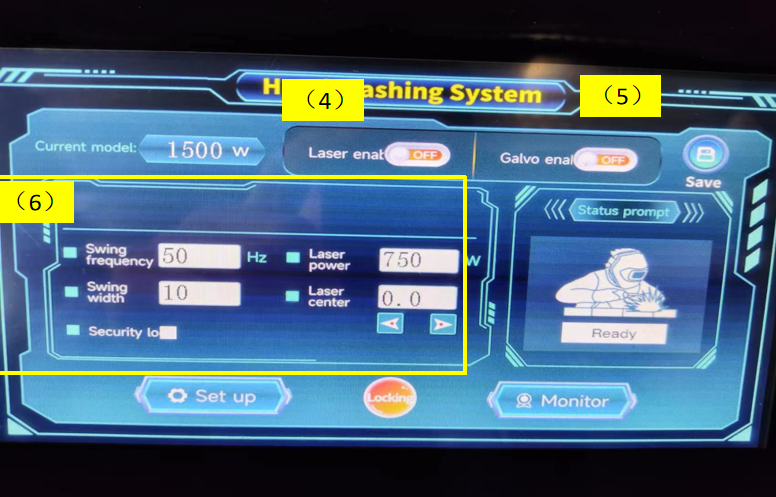
Common troubleshooting
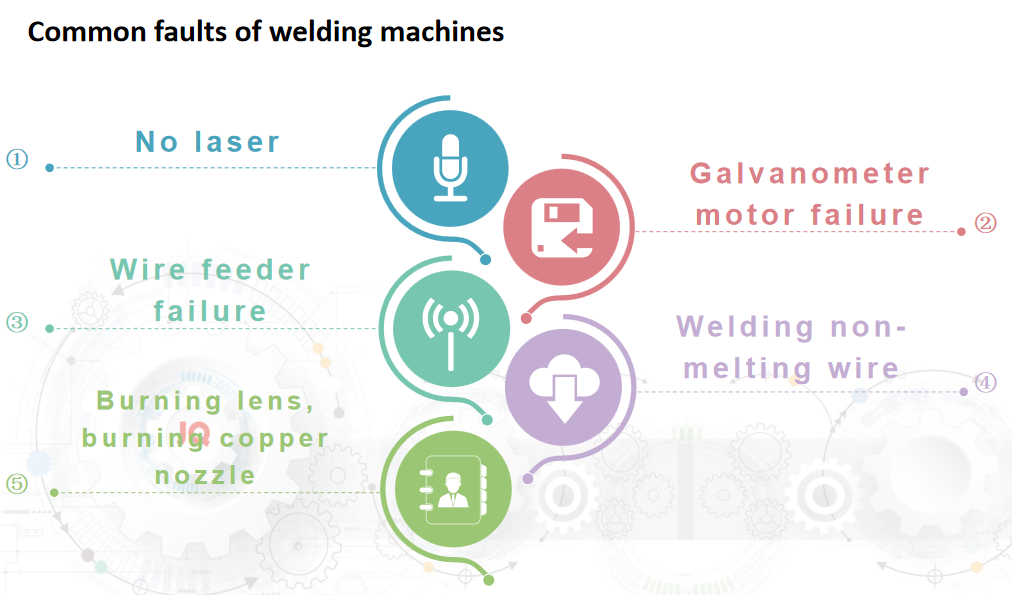
Troubleshooting laser problems that don’t work
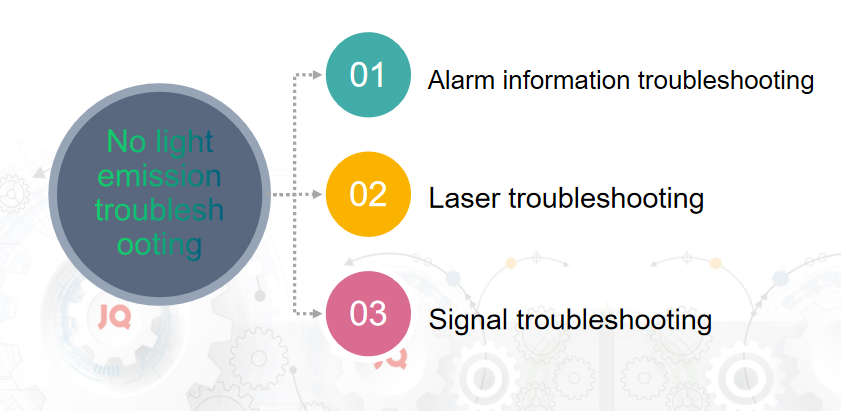
Chiller alarm
Troubleshoot according to the chiller alarm code. Common faults:
High temperature alarm
① The dust filter is clogged and the heat dissipation is poor.
② The air outlet is poor in heat dissipation.
③The compressor is broken
④Confirm the power frequency
Flow Alarms
①The water volume in the water tank is too low
②The water pump is broken
③The flow meter is broken
④The water circulation pipeline is blocked or the water pipe is bent and deformed.
Laser source alarm
- Common alarm information;
- Laser password expires
- QBH alarm
- Voltage alarm
System alarm information
- Is the light enable switch turned on?
- System permissions expire
- Chiller alarm
- Communication alarm
Laser troubleshooting
Powering up the laser
- Laser power cord wiring confirmation
- Confirm the power supply voltage
- Confirm the status of the chiller
- Confirm that the control line is short-circuited
- Laser emergency stop confirmation
- Confirmation of chiller signal line
Red light status confirmation
- After the laser is powered on, check whether there is red light Look through the tail of the welding gun to see if there is red light.
- Lens status confirmation
- Fiber breakage
Wiring and setting confirmation
- Laser control line wiring confirmation
- Confirmation of control line continuity
- Confirm the internal settings of the laser
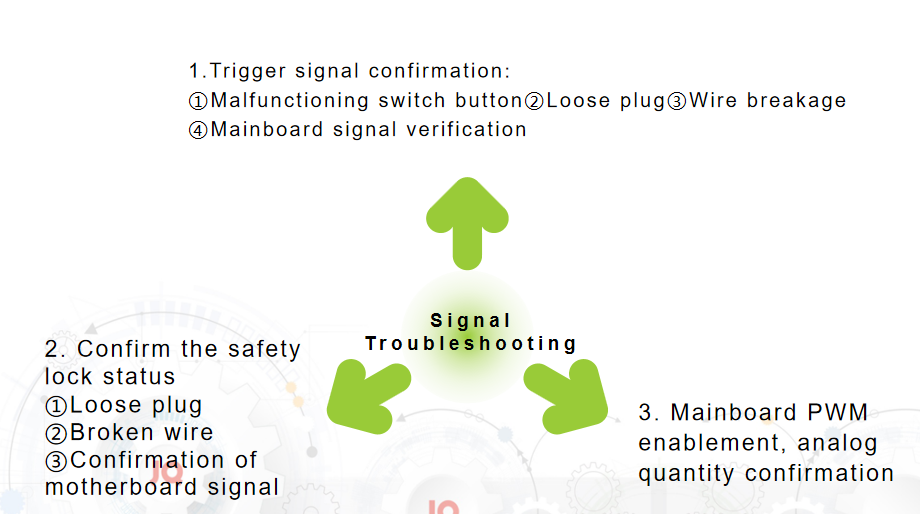
Wire feeder does not feed wire
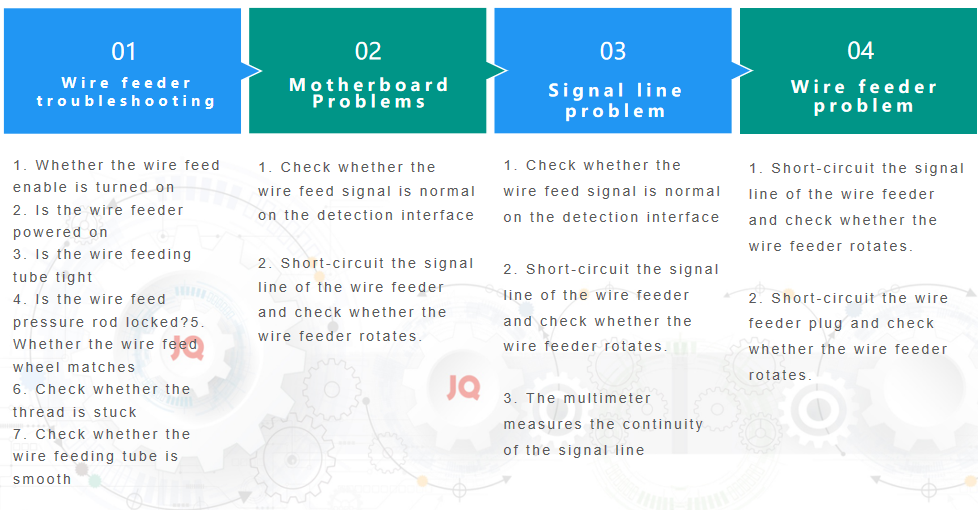
Troubleshooting wire not melting
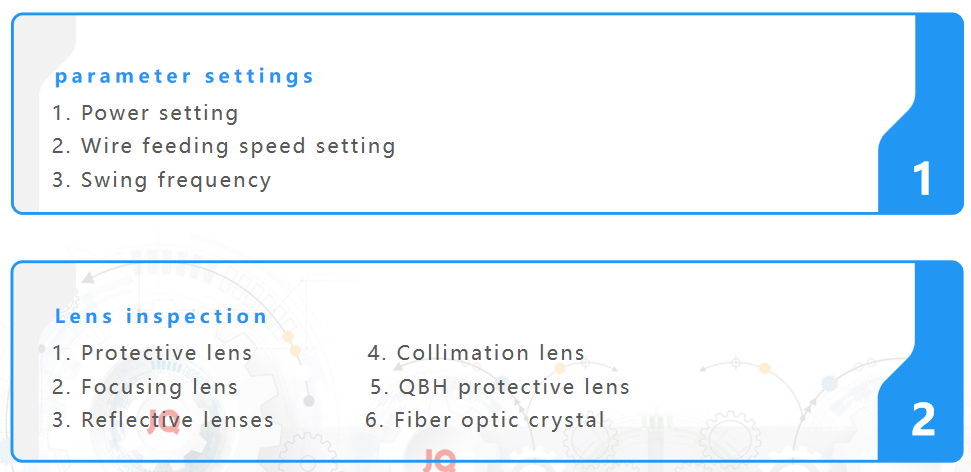