Platform laser welding has emerged as a transformative technology in the realm of automated production lines, revolutionizing the way manufacturers approach welding processes. This advanced method utilizes focused laser beams to join materials with high precision and efficiency, making it an essential tool in various industries, including automotive, aerospace, and electronics. The significance of platform laser welding lies in its ability to enhance productivity, improve weld quality, and reduce operational costs. As industries strive for greater efficiency and quality in their manufacturing processes, the adoption of platform laser welding is becoming increasingly prevalent.The use of laser welding technology is not just about replacing traditional methods; it represents a paradigm shift in how welding can be integrated into automated systems. With the ability to automate complex welding tasks, manufacturers can achieve higher levels of consistency and reliability. This is particularly crucial in industries where safety and performance are paramount, such as aerospace and automotive sectors. The precision offered by laser welding ensures that components are joined with minimal defects, which can significantly impact the performance and longevity of the final product.
Benefits of Platform Laser Welding
- High Precision: The focused laser beam allows for accurate control over the heat input, resulting in precise and consistent welds. This is particularly beneficial for applications requiring tight tolerances. In traditional welding methods, variations in heat distribution can lead to inconsistencies in weld quality. However, with platform laser welding, the ability to focus the beam down to a very small diameter means that manufacturers can achieve welds that meet stringent specifications without the need for extensive post-weld processing.
- Speed and Efficiency: Laser welding is significantly faster than traditional methods. Automated systems can perform rapid and continuous welding, leading to higher throughput and reduced production costs. The speed of laser welding not only increases productivity but also allows for shorter cycle times in manufacturing processes. This efficiency translates directly into cost savings for companies as they can produce more products in less time while maintaining high-quality standards.
- Versatility: Platform laser welders can handle a variety of materials, including metals and plastics. They are capable of welding different thicknesses and combinations of materials, making them suitable for diverse applications. This versatility is crucial as manufacturers often work with multiple materials across different projects. The ability to adapt the laser welding process to various materials without significant changes to equipment or processes enhances overall operational flexibility.
- Minimal Heat Affected Zone (HAZ): The concentrated heat source results in a minimal HAZ around the weld area. This reduces the risk of material distortion and preserves the mechanical properties of surrounding materials. In many applications, particularly those involving sensitive components or high-performance materials, maintaining the integrity of the base material is essential. The reduced HAZ also means less need for additional finishing processes, further streamlining production.
- Consistent Weld Quality: Automated platform laser welding ensures uniform welds throughout production, eliminating variations commonly associated with manual welding. This consistency is vital for industries where even minor defects can lead to significant failures or safety issues. By employing automated systems that utilize laser technology, manufacturers can ensure that every weld meets predetermined quality standards.
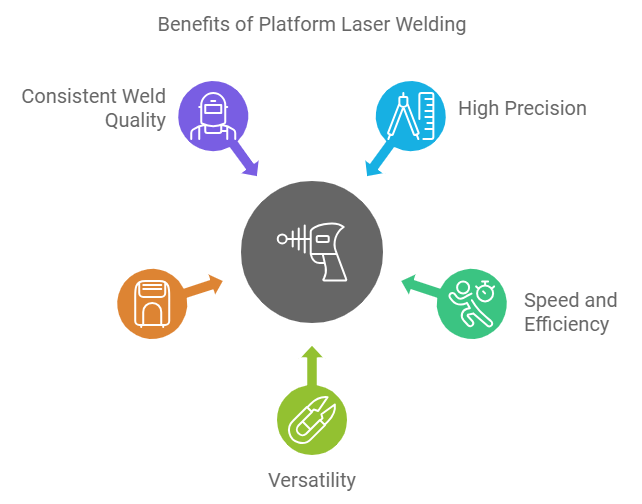
Key Components of Automated Laser Welding Systems
Automated laser welding systems consist of several critical components that work together to achieve optimal performance:
ComponentDescriptionLaser SourceGenerates the focused laser beam required for welding.Beam Delivery SystemTransmits the laser beam to the workpiece through optical fibers or mirrors.Control SystemManages and optimizes the entire welding process for consistency and quality.Workpiece Manipulation SystemPositions materials accurately during the welding process.Cooling SystemMaintains optimal operating temperatures for the laser source and components.
Trends in Platform Laser Welding
The landscape of platform laser welding is continually evolving due to advancements in technology. Some notable trends include:
- Increased Automation: The integration of robotics and AI enhances the automation capabilities of laser welding systems, allowing for real-time adjustments based on feedback from sensors. As manufacturers seek to streamline operations further, automated systems that can adapt on-the-fly will become increasingly valuable.
- Collaborative Robots (Cobots): Cobots are designed to work alongside human operators safely. They enhance efficiency by performing repetitive tasks while humans focus on complex operations. This collaboration not only boosts productivity but also allows skilled workers to engage more deeply with tasks that require critical thinking or creativity.
- Data-Driven Optimization: The use of data analytics allows manufacturers to optimize welding parameters based on historical data, improving overall efficiency and quality. By analyzing past performance data, companies can identify patterns that lead to defects or inefficiencies and adjust their processes accordingly.
- Adaptive Control Systems: These systems adjust welding parameters dynamically based on real-time feedback from the environment, ensuring consistent quality even in variable conditions. Such adaptability is crucial in environments where material properties may change due to factors like temperature fluctuations or humidity levels.
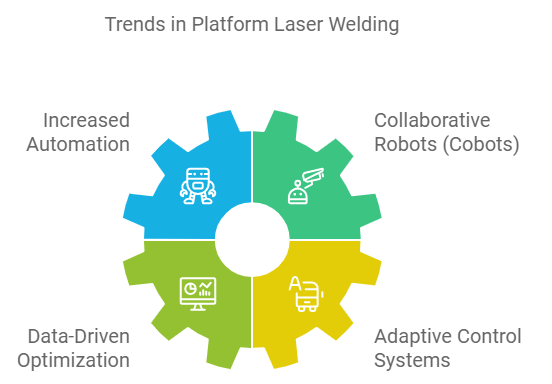
Applications Across Industries
Platform laser welding is utilized across various sectors due to its versatility and efficiency:
- Automotive Industry: Used for joining components in vehicle assembly, ensuring lightweight structures without compromising strength.
- Aerospace Sector: Essential for fabricating critical components that require high precision and reliability under extreme conditions.
- Electronics Manufacturing: Ideal for assembling delicate electronic components where precision is paramount.
Challenges in Implementation
Despite its advantages, several challenges may arise when integrating platform laser welding into production lines:
- Initial Investment Costs: The upfront costs associated with purchasing advanced laser welding equipment can be significant. While long-term savings may offset these costs through increased efficiency and reduced waste, many companies face budget constraints that make initial investments challenging.
- Integration with Existing Systems: Compatibility issues with legacy systems may hinder seamless implementation. Manufacturers must often invest time and resources into retrofitting existing equipment or training personnel on new technologies.
- Skilled Workforce Requirement: Operating advanced automated systems requires specialized training, which may not be readily available in all manufacturing environments. Companies must invest in workforce development initiatives to ensure employees have the necessary skills to operate sophisticated machinery effectively.
Future Outlook
The future of platform laser welding looks promising as technology continues to advance. Key developments expected include:
- Enhanced Laser Technologies: Innovations such as multi-wavelength lasers will expand the range of materials that can be effectively welded.
- Integration with Industry 4.0: The convergence of IoT technologies with laser welding will facilitate smarter manufacturing processes through real-time monitoring and data-driven decision-making.
- Sustainability Initiatives: As industries move towards greener practices, laser welding’s energy efficiency will play a crucial role in reducing carbon footprints during manufacturing processes.
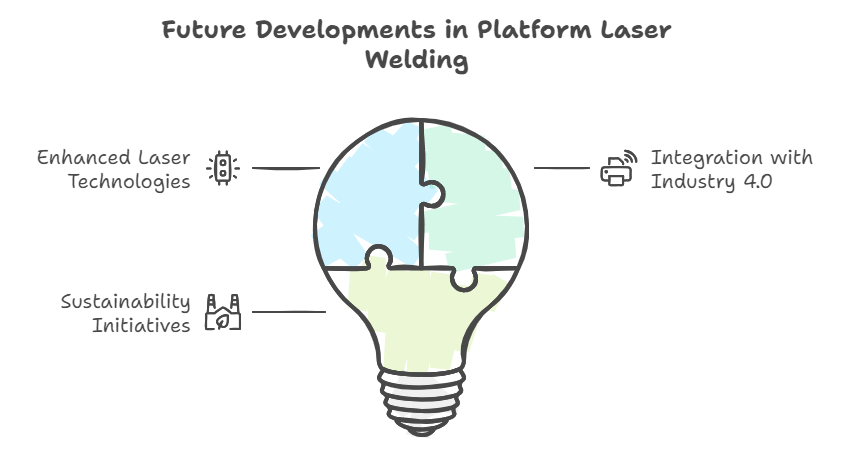
Conclusion
Platform laser welding represents a significant advancement in automated production lines, offering unparalleled precision, speed, and flexibility. Its application across various industries underscores its importance as a key technology for modern manufacturing processes. As advancements continue to emerge, platform laser welding will undoubtedly play a central role in shaping the future of industrial automation.