In the ever-evolving world of automotive manufacturing, innovation has been a constant driving force. One such innovation that has gained substantial traction in recent years is laser welding. This cutting-edge technology has revolutionized the way cars are built, offering a wide range of benefits while also presenting unique challenges. In this article, we will delve into the world of laser welding in automotive manufacturing, exploring its advantages and addressing the hurdles it brings to the table.
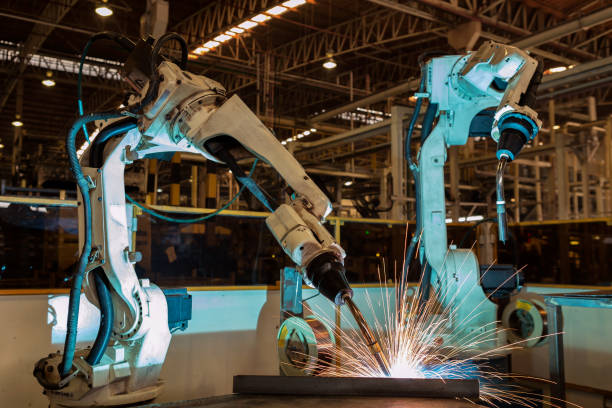
1. Introduction to Laser Welding
Laser welding is a cutting-edge welding technique that employs a highly concentrated laser beam to join two or more materials together. This method has gained prominence in various industries, including automotive manufacturing, due to its precision and efficiency.
2. Why Laser Welding in Automotive Manufacturing?
Automobiles demand a high degree of precision and reliability in their construction. Laser welding fits the bill perfectly, offering numerous advantages that make it an ideal choice for the automotive industry.
3. Benefits of Laser Welding
3.1 Precision and Accuracy
Laser welding provides unparalleled precision, resulting in strong and consistent welds. This level of accuracy is crucial in ensuring the structural integrity of automotive components.
3.2 Reduced Heat Affected Zone (HAZ)
Compared to traditional welding methods, laser welding produces a significantly smaller heat affected zone. This minimizes the risk of material distortion and ensures the integrity of sensitive vehicle parts.
3.3 Improved Aesthetics
The clean and narrow weld seams created by laser welding enhance the visual appeal of automotive components, which is especially important for high-end and luxury vehicles.
3.4 Enhanced Durability
Laser welds exhibit exceptional strength and durability, ensuring that vehicles can withstand the rigors of daily use and various environmental conditions.
4. Challenges of Laser Welding
4.1 High Initial Investment
Implementing laser welding technology in an automotive manufacturing facility requires a substantial initial investment in equipment and training.
4.2 Skilled Workforce Requirements
Operating laser welding machines demands a skilled and well-trained workforce, which can be a challenge for some manufacturers.
4.3 Material Compatibility
Laser welding is highly effective on certain materials but may pose challenges with materials that are less responsive to this technique.
4.4 Surface Preparation
Proper surface preparation is critical for successful laser welding. Any contaminants or inconsistencies can negatively impact weld quality.
5. Laser Welding Techniques
There are various laser welding techniques employed in the automotive industry, each tailored to specific applications and materials.
6. Applications in the Automotive Industry
Laser welding finds applications in various automotive components, including body panels, exhaust systems, and battery packs in electric vehicles.
7. Future Trends in Laser Welding
The future of laser welding in automotive manufacturing looks promising, with ongoing research aimed at improving efficiency and reducing costs.
8. Sustainability and Environmental Impact
Laser welding’s precision and minimal waste production contribute to a more sustainable manufacturing process, aligning with the automotive industry’s green initiatives.
9. Conclusion
In conclusion, laser welding has emerged as a game-changer in automotive manufacturing. Its benefits in terms of precision, reduced HAZ, improved aesthetics, and durability make it a top choice for manufacturers looking to enhance the quality of their vehicles. However, the challenges of high initial investment, workforce training, material compatibility, and surface preparation cannot be ignored. As the industry continues to evolve, laser welding is poised to play a pivotal role in shaping the future of automotive manufacturing.