1. Introduction to Laser Welding Technology in Aerospace
Laser welding has emerged as a transformative technology in the aerospace sector, offering precise and efficient solutions for joining intricate and critical aircraft components. Unlike conventional welding methods, laser welding employs a concentrated beam of high-energy photons to melt and fuse metals with minimal heat-affected zones. This precision minimizes distortion and material damage, making it particularly suitable for the aerospace industry, where structural integrity and weight reduction are paramount.
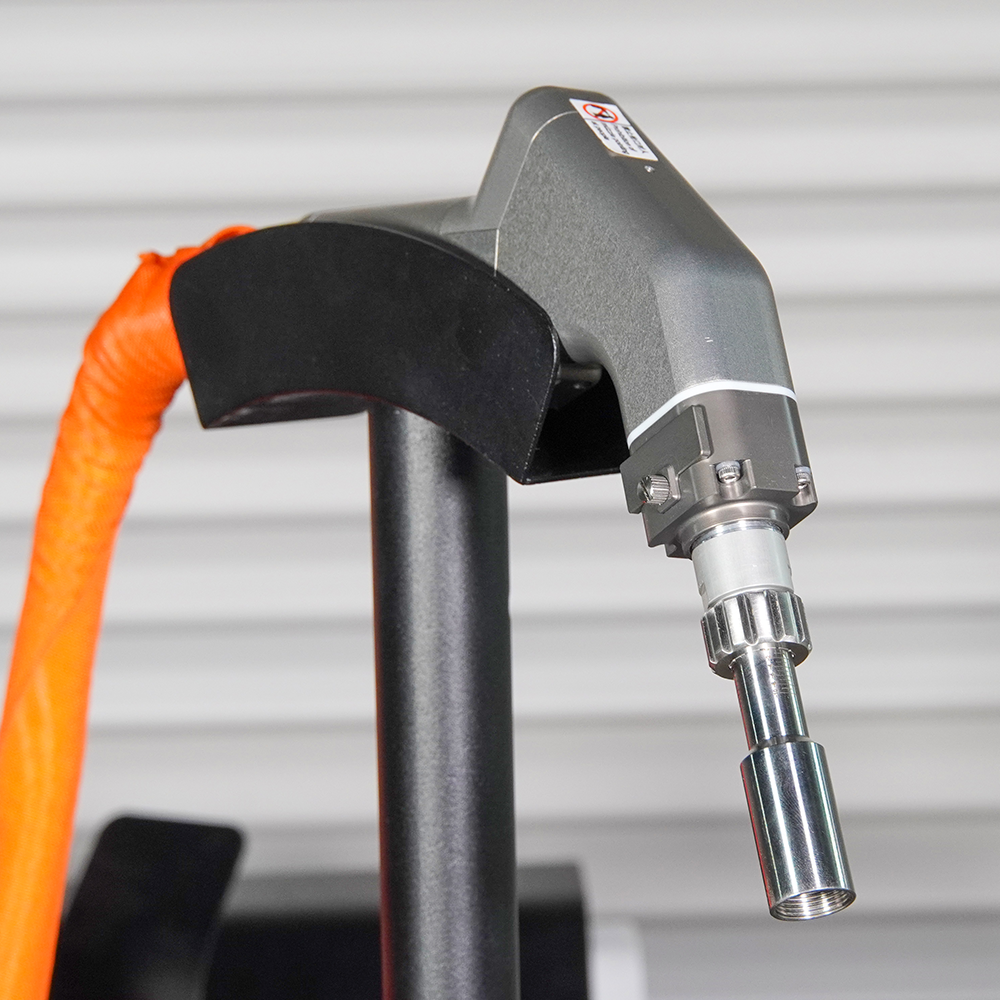
2. Advantages of Laser Welding for Aircraft Components
The utilization of laser welding machines in aircraft component manufacturing offers a host of advantages. First, the pinpoint accuracy of laser beams ensures that delicate components, such as turbine blades and engine housings, maintain their intricate geometries. Second, the minimal heat input mitigates the risk of distortion, preserving the structural integrity of the components. Additionally, the non-contact nature of laser welding eliminates the need for physical pressure, reducing the likelihood of deformation or stress-induced defects.
3. Challenges and Solutions for Implementing Laser Welding in Aerospace
While laser welding holds great promise, its implementation in aerospace isn’t devoid of challenges. One such challenge is the management of thermal gradients and residual stresses that can result from rapid heating and cooling cycles. Innovative cooling strategies and precise control of laser parameters have been developed to mitigate these effects. Furthermore, ensuring consistent weld quality across various material combinations demands meticulous calibration of laser settings and material compatibility assessments.
4. Case Studies: Successful Applications of Laser Welding in Aircraft Manufacturing
Several notable case studies showcase the efficacy of laser welding in aircraft manufacturing. One example is the welding of titanium-aluminum hybrid structures in modern aircraft, where the precise control of heat input and metallurgical interactions is crucial. Laser welding has enabled the seamless joining of these dissimilar materials, reducing weight and enhancing fuel efficiency.
5. Precision and Reliability: Ensuring Quality Welds in Aircraft Parts
Precision and reliability are paramount in aerospace applications, and laser welding delivers on both fronts. The non-contact nature of laser welding eliminates the risk of contamination, ensuring clean welds. Moreover, the digital control and monitoring systems in modern laser welding machines allow real-time adjustments to welding parameters, guaranteeing consistency and quality in every joint.
6. Innovative Design Possibilities Enabled by Laser Welding in Aerospace
Laser welding’s ability to create strong, intricate joints opens the door to innovative design possibilities in aerospace. Complex and lightweight structures, which were previously challenging to fabricate using traditional methods, can now be realized. The precise energy deposition of laser welding facilitates the creation of intricate lattice structures, optimizing strength-to-weight ratios and enhancing overall component performance.
7. Material Compatibility and Metallurgical Considerations in Laser Welding
Successful laser welding in aerospace necessitates a deep understanding of material compatibility and metallurgical interactions. Unlike conventional welding, which might involve the addition of filler material, laser welding relies on the fusion of base materials. This demands precise control over composition, grain structure, and phase transformations, ensuring the final joint meets stringent aerospace standards for strength and durability.
8. Safety Measures and Regulations in Laser Welding for Aerospace Components
As with any advanced technology, safety remains paramount in laser welding for aerospace applications. Stringent safety measures are in place to protect operators from exposure to high-intensity laser radiation. Moreover, compliance with aviation regulations and standards is crucial to ensure that laser-welded components meet rigorous quality and reliability criteria.
9. Comparative Analysis: Laser Welding vs. Traditional Welding Techniques in Aviation
Comparing laser welding with traditional welding techniques reveals significant differences. Traditional methods often involve more extensive heat input, which can lead to distortion and undesirable metallurgical changes. Laser welding’s ability to focus energy precisely reduces these effects, resulting in stronger, more consistent welds. Additionally, the automated nature of laser welding enhances efficiency, reducing production time and costs.
10. Future Trends: Advancements and Research Directions in Laser Welding for Aircraft Components
The future of laser welding in aerospace holds exciting prospects. Ongoing research aims to optimize laser welding parameters for emerging materials, such as advanced composites and high-temperature alloys. Integration with advanced robotics and AI-driven systems is expected to further enhance precision and productivity. As the aerospace industry evolves, laser welding’s role will undoubtedly expand, enabling the creation of safer, more efficient, and technologically advanced aircraft components.