Laser welding has revolutionized the manufacturing industry with its precision and efficiency. However, it’s not all smooth sailing in the world of laser welding. The intense heat generated during the process can lead to several thermal issues, the most prominent being the Heat-Affected Zone (HAZ). In this article, we’ll dive deep into the world of laser welding and explore strategies to effectively deal with the HAZ and other thermal challenges it presents.
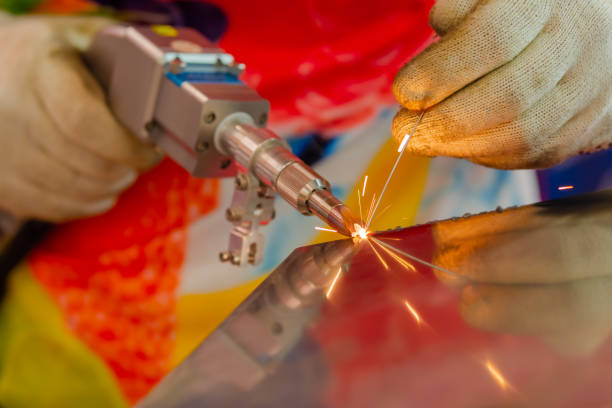
Introduction
Understanding the Basics of Laser Welding
Laser welding, a non-contact joining process, employs a highly focused beam of light to melt and fuse materials together. Its popularity stems from its pinpoint accuracy and minimal distortion. However, the very thing that makes laser welding efficient is also the source of its thermal challenges – extreme heat.
The Heat-Affected Zone (HAZ)
What is the HAZ?
The HAZ is a region surrounding the weld where the temperature was elevated but didn’t reach its melting point. This can cause changes in material properties, leading to potential weaknesses in the weld joint.
Factors Affecting HAZ
Factors like laser power, welding speed, and material thickness play a crucial role in determining the size and severity of the HAZ. It’s essential to strike a balance between these parameters.
Thermal Issues in Laser Welding
Beyond the HAZ: Other Thermal Challenges
Apart from the HAZ, laser welding can introduce other problems such as cracking, distortion, and porosity. These issues can compromise the integrity of the welded components.
Mitigating Thermal Issues
Cooling Systems and Their Role
Effective cooling systems are essential in laser welding to dissipate heat quickly. Water or gas cooling can prevent overheating and minimize the size of the HAZ.
Controlling Laser Parameters
Fine-tuning laser parameters like beam focus and pulse duration can help manage heat input, ensuring a more controlled welding process.
Materials Matter
Selecting the Right Materials
Not all materials are created equal when it comes to laser welding. Some are more sensitive to heat than others. The choice of material can significantly impact the thermal issues you encounter.
Advanced Techniques
Strategies for Heat Dissipation
Advanced techniques like beam oscillation and beam shaping can help distribute heat more evenly, reducing the chances of thermal defects.
Quality Control
Inspecting and Testing for Thermal Defects
Thermal issues may not always be visible to the naked eye. Employing quality control measures such as non-destructive testing can catch defects early on.
Safety First
Ensuring Worker Safety
Laser welding involves intense heat and potentially harmful emissions. Proper safety measures, including protective gear and ventilation, are vital to safeguard workers.
Cost Considerations
Balancing Efficiency and Expense
While laser welding offers numerous advantages, it’s essential to weigh the cost of equipment and maintenance against the benefits of precision and efficiency.
Future of Laser Welding
Innovations on the Horizon
The world of laser welding continues to evolve. Keep an eye out for emerging technologies like hybrid welding and automation that promise even greater control over thermal issues.
Conclusion
Mastering the Heat in Laser Welding
The heat may be on in laser welding, but with the right knowledge and techniques, you can stay cool under pressure. Understanding the HAZ and other thermal challenges, along with employing effective mitigation strategies, is key to achieving flawless laser welds.