In the ever-evolving world of manufacturing and fabrication, laser welding machines have become an indispensable tool. These precision instruments use high-intensity laser beams to join metals with unparalleled accuracy and speed. However, like any sophisticated machinery, laser welding machines require regular maintenance to ensure optimal performance and longevity. In this comprehensive guide, we will explore the essential aspects of maintaining a laser welding machine, covering everything from routine checks to troubleshooting common issues.
Introduction
Laser welding technology has revolutionized the manufacturing industry, allowing for precise and efficient metal joining. However, to reap the full benefits of laser welding, it’s crucial to understand the maintenance requirements of these machines.
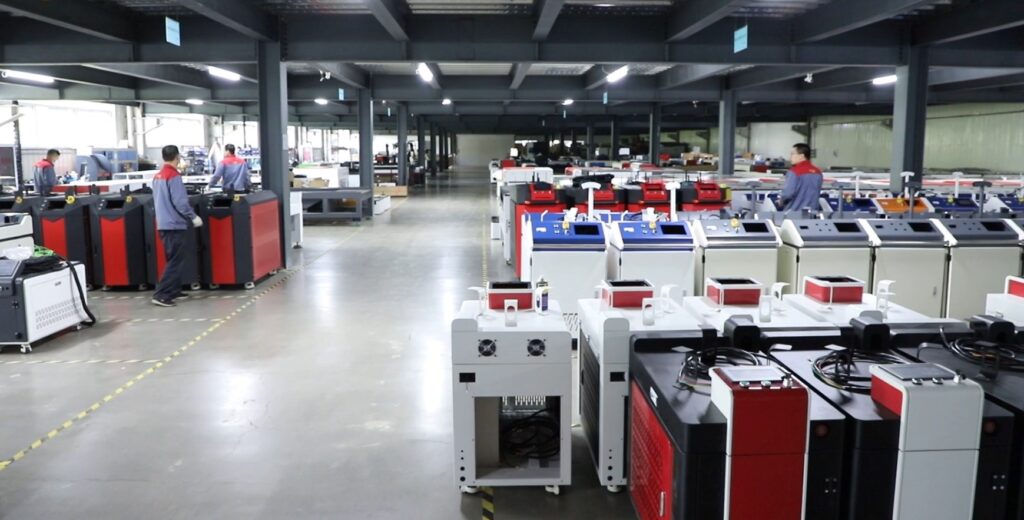
Understanding Laser Welding
2.1 How Laser Welding Works
Laser welding involves the use of a highly concentrated laser beam to melt and fuse metals together. This process generates intense heat, resulting in a strong and precise weld.
2.2 Types of Laser Welding Machines
There are various types of laser welding machines, including fiber laser welders, CO2 laser welders, and Nd:YAG laser welders, each with its unique characteristics.
Importance of Maintenance
3.1 Prolonging Machine Lifespan
Regular maintenance significantly extends the lifespan of your laser welding machine, protecting your investment for years to come.
3.2 Ensuring Safety
Proper maintenance is crucial for ensuring the safety of operators and preventing accidents that can occur due to neglected machinery.
Regular Inspection
4.1 Checking Optics
Regularly inspecting and cleaning the optical components of the laser system prevents beam distortion and ensures precise welding.
4.2 Inspecting Cooling Systems
Adequate cooling is vital to prevent the laser system from overheating. Check the cooling system regularly for any issues.
4.3 Examining Gas Supply
Gas supply is essential for creating a stable welding environment. Inspect gas lines and regulators to prevent leaks.
Cleaning and Calibration
5.1 Cleaning the Optical Components
Dust and debris can accumulate on optical components, affecting the quality of the laser beam. Regular cleaning is essential.
5.2 Calibrating the Laser Beam
Periodic calibration ensures that the laser beam remains focused and accurate, resulting in high-quality welds.
Safety Measures
6.1 Protective Gear
Operators should always wear appropriate protective gear, including safety glasses and gloves, when working with laser welding machines.
6.2 Proper Ventilation
Maintain proper ventilation in the workspace to dissipate fumes and ensure a safe working environment.
Common Issues and Troubleshooting
7.1 Beam Misalignment
If you notice inconsistent welds or reduced precision, beam misalignment may be the issue. Refer to the user manual for alignment instructions.
7.2 Gas Leaks
Gas leaks can disrupt the welding process. Inspect gas lines and connections for leaks and repair them promptly.
7.3 Cooling System Problems
If the cooling system fails, the laser machine can overheat. Check for coolant leaks and ensure pumps are functioning correctly.
Professional Maintenance
8.1 Scheduled Servicing
Consider scheduling routine maintenance with a qualified technician who can identify and address potential issues.
8.2 Hiring a Laser Technician
In complex cases, it’s advisable to hire a specialized laser technician for maintenance and repairs.
Conclusion
Proper maintenance of your laser welding machine is essential for its longevity and the quality of your work. By following these guidelines and addressing issues promptly, you can ensure smooth operations and a safer working environment.