1. Introduction
Laser welding has revolutionized the manufacturing industry with its ability to produce high-quality welds in a wide range of materials. It uses a concentrated beam of light to melt and fuse the workpieces, resulting in precise and clean welds. Choosing the right laser welding machine is crucial to ensure optimal performance and efficiency in your business operations.
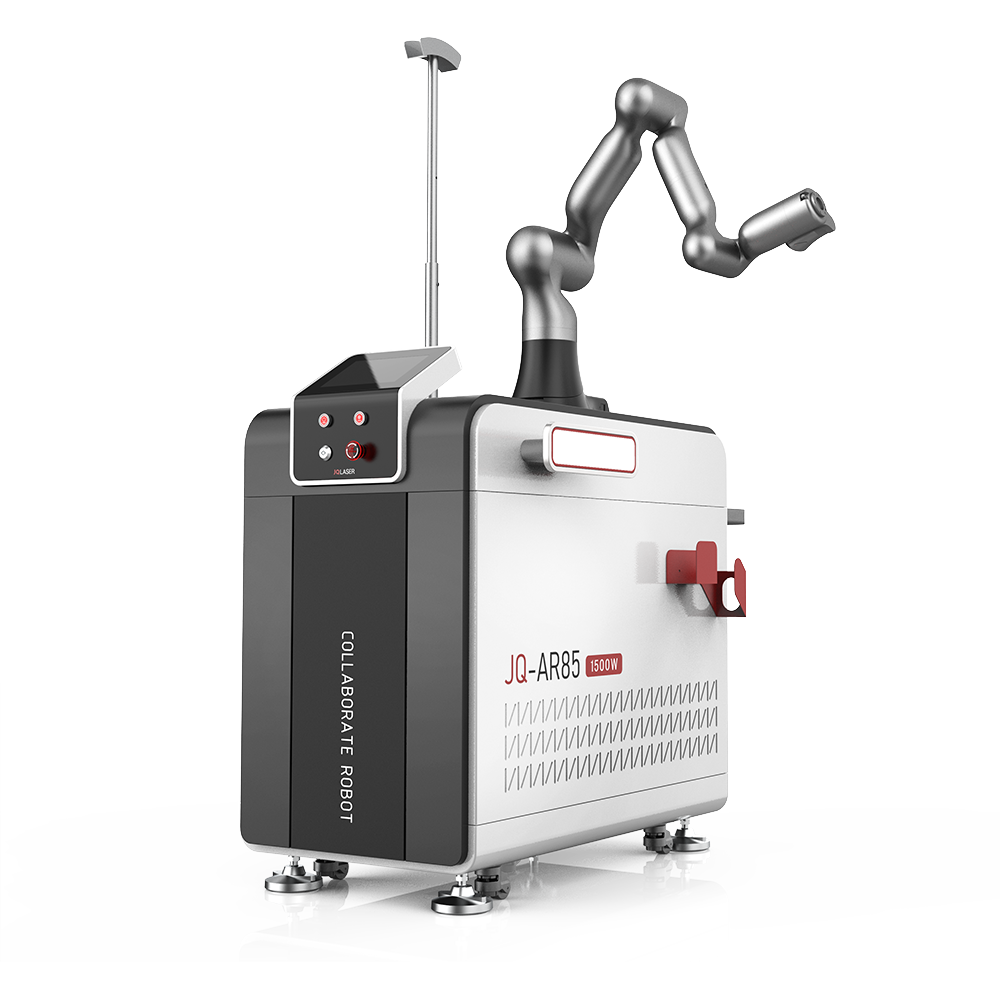
2. Understanding Laser Welding
Before delving into the selection process, it’s important to have a basic understanding of laser welding. Laser welding utilizes a focused laser beam to heat and join two or more pieces of metal together. The laser beam creates a narrow, highly intense heat source, which melts the workpieces, allowing them to bond together when cooled. This process offers numerous advantages over traditional welding methods, such as reduced heat distortion, minimal post-welding cleanup, and the ability to weld intricate and delicate components.
3. Assessing Your Business Requirements
To choose the right laser welding machine, you need to assess your business requirements thoroughly. Consider factors such as the types of materials you work with, the desired welding speed, the complexity of your welding projects, and any specific industry standards or regulations you must comply with. This evaluation will help you determine the key features and capabilities your laser welding machine should have.
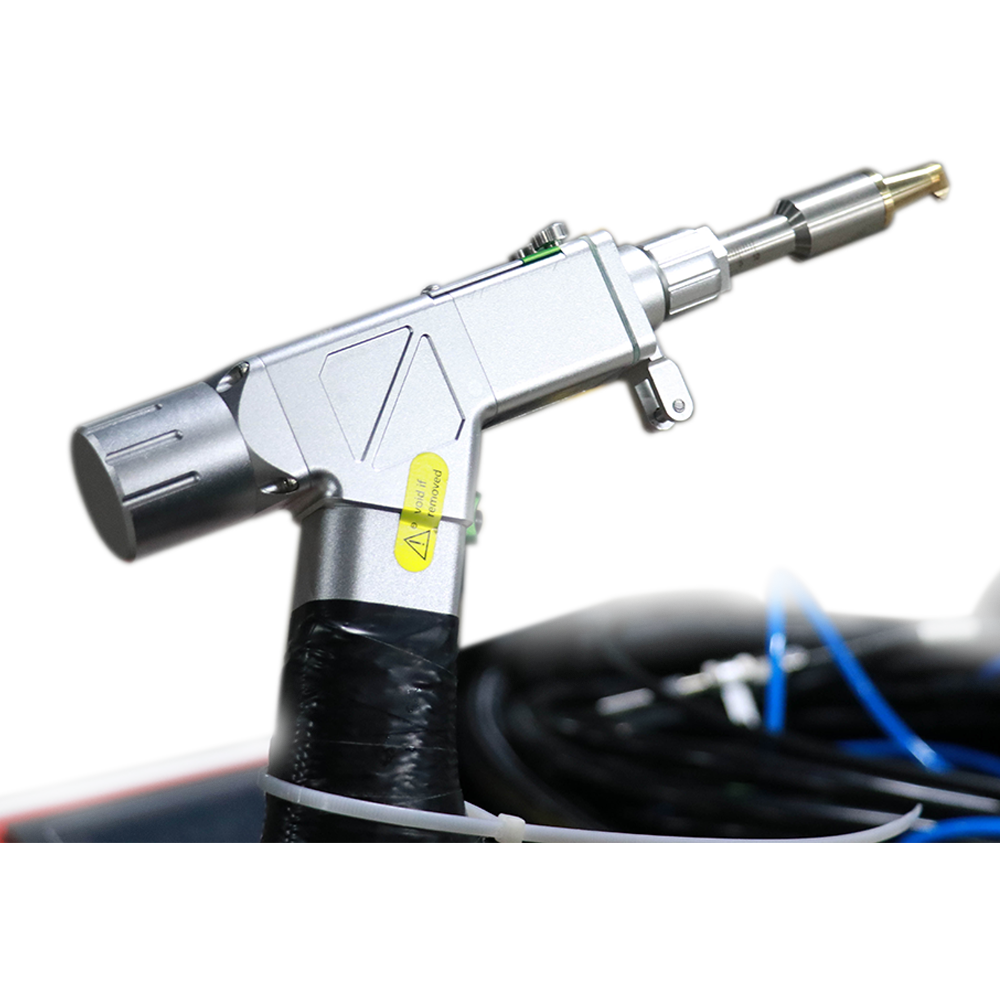
4. Types of Laser Welding Machines
There are several types of laser welding machines available in the market. Each type has its own strengths and limitations, making it important to understand their differences before making a decision.
4.1 Fiber Laser Welding Machines
Fiber laser welding machines are known for their high energy efficiency and precise welding capabilities. They use fiber optics to deliver the laser beam, resulting in excellent beam quality and stability. Fiber laser welding machines are suitable for a wide range of applications, including welding thin materials and conducting deep welds with minimal heat input.
4.2 CO2 Laser Welding Machines
CO2 laser welding machines utilize a carbon dioxide gas mixture to generate the laser beam. They are commonly used for welding thicker materials and have a higher penetration depth compared to fiber laser welding machines. CO2 laser welding machines are known for their versatility and are often preferred for industrial applications.
4.3 Nd:YAG Laser Welding Machines
Nd:YAG (Neodymium-doped Yttrium Aluminum Garnet) laser welding machines offer a good balance between power and precision. They are suitable for welding a variety of materials, including metals, plastics, and ceramics. Nd:YAG laser welding machines are often chosen for applications that require a combination of high welding speed and fine control.
5. Key Factors to Consider
When choosing a laser welding machine, there are several key factors you should consider to ensure the best fit for your business requirements.
5.1 Power and Energy Output
The power and energy output of a laser welding machine determine its welding capabilities. Higher power allows for faster and deeper welds, while lower power may be sufficient for thinner materials. Assess the power and energy requirements of your welding projects to determine the appropriate machine for your needs.
5.2 Beam Quality
The beam quality affects the precision and stability of the laser welding process. A high-quality beam produces consistent welds with minimal defects. Be sure to evaluate the beam quality specifications of the machines you are considering.
5.3 Welding Speed
Welding speed is an essential factor, especially if you have high-volume production requirements. A laser welding machine with faster welding speed can significantly improve your productivity and reduce cycle times. Consider the desired welding speed for your applications and choose a machine that can meet those requirements.
5.4 Material Compatibility
Different laser welding machines have varying degrees of compatibility with different materials. Ensure that the machine you select can effectively weld the materials commonly used in your business. Factors such as material thickness, reflectivity, and thermal conductivity can influence the welding process.
5.5 Automation and Integration
Automation and integration capabilities are crucial for streamlining your manufacturing processes. Look for laser welding machines that offer automation features such as robotic arms, CNC interfaces, and integrated inspection systems. These features can enhance productivity and reduce manual labor.
5.6 Maintenance and Support
Consider the maintenance requirements and available support for the laser welding machines you are considering. Regular maintenance is essential to keep the machine in optimal condition and minimize downtime. Additionally, ensure that the supplier provides timely support, training, and spare parts to address any issues that may arise.
6. Evaluating the Cost
While the initial cost of a laser welding machine is an important consideration, it’s equally important to evaluate the overall cost of ownership throughout its lifespan. Consider the following cost aspects:
6.1 Initial Investment
The initial cost of the machine includes the purchase price, installation, and setup expenses. Compare the prices of different machines while considering their features, capabilities, and reputation.
6.2 Operational Costs
Operational costs include factors such as energy consumption, maintenance expenses, and consumables. Energy-efficient machines can help reduce long-term operational costs. Additionally, consider the availability and cost of spare parts and consumables specific to the machine.
6.3 Return on Investment (ROI)
Assess the potential return on investment (ROI) when choosing a laser welding machine. Consider the time saved, increased productivity, improved quality, and reduced rework or scrap. A machine with a higher upfront cost but significant productivity gains may offer a better ROI in the long run.
7. Choosing the Right Supplier
Selecting a reputable and reliable supplier is crucial to ensure a smooth purchasing experience and ongoing support. Consider the following factors when evaluating suppliers:
7.1 Reputation and Experience
Choose a supplier with a good reputation and extensive experience in the laser welding industry. Look for customer reviews, testimonials, and case studies to gauge their track record.
7.2 Customer Support and Training
Ensure that the supplier offers comprehensive customer support and training programs. A supplier who provides training on machine operation, maintenance, and troubleshooting can help you maximize the potential of your laser welding machine.
7.3 Warranty and Service Agreements
Review the warranty terms and service agreements provided by the supplier. Understand the coverage and duration of the warranty, as well as the availability of service technicians in your area. A reliable warranty and service support can provide peace of mind and minimize downtime.
8. Conclusion
Choosing the right laser welding machine for your business is a crucial decision that can significantly impact your manufacturing processes. By assessing your business requirements, understanding the different types of laser welding machines, considering key factors such as power, beam quality, welding speed, material compatibility, automation, and maintenance, and evaluating the overall cost and supplier reputation, you can make an informed decision that aligns with your needs and goals.
9. FAQs
FAQ 1: Can laser welding be used for all types of materials?
Laser welding is versatile and can be used for various materials, including metals, plastics, and ceramics. However, the suitability of laser welding for specific materials depends on factors such as material thickness, reflectivity, and thermal conductivity.
FAQ 2: How does laser welding compare to traditional welding methods?
Laser welding offers several advantages over traditional welding methods, such as reduced heat distortion, minimal post-welding cleanup, and the ability to weld intricate and delicate components. It also provides precise control and high welding speeds.
FAQ 3: What safety measures should be taken when using laser welding machines?
When using laser welding machines, it is essential to follow safety protocols to protect operators and ensure a safe working environment. This includes wearing appropriate protective eyewear, implementing safety interlocks, and providing proper training on machine operation and safety procedures.
FAQ 4: Can laser welding machines be customized for specific applications?
Yes, laser welding machines can often be customized or adapted for specific applications. Discuss your requirements with the supplier to explore customization options that can optimize the machine for your specific needs.
FAQ 5: Is it possible to upgrade a laser welding machine in the future?
Depending on the specific machine and its design, it may be possible to upgrade certain components or features in the future. However, it is important to consult with the supplier regarding upgrade options and compatibility to ensure a smooth transition.