1 Overview of laser welding technology
1.1 Working principle of laser welding technology Laser welding machine is a device that applies laser technology to the field of welding. Generally speaking, laser technology uses a polarizer to reflect the beam generated by the laser and focus it in a focusing device, ultimately forming a high-energy beam. When the focus is close to the workpiece, the workpiece will instantly melt and evaporate in just a few milliseconds, thus realizing the welding process.
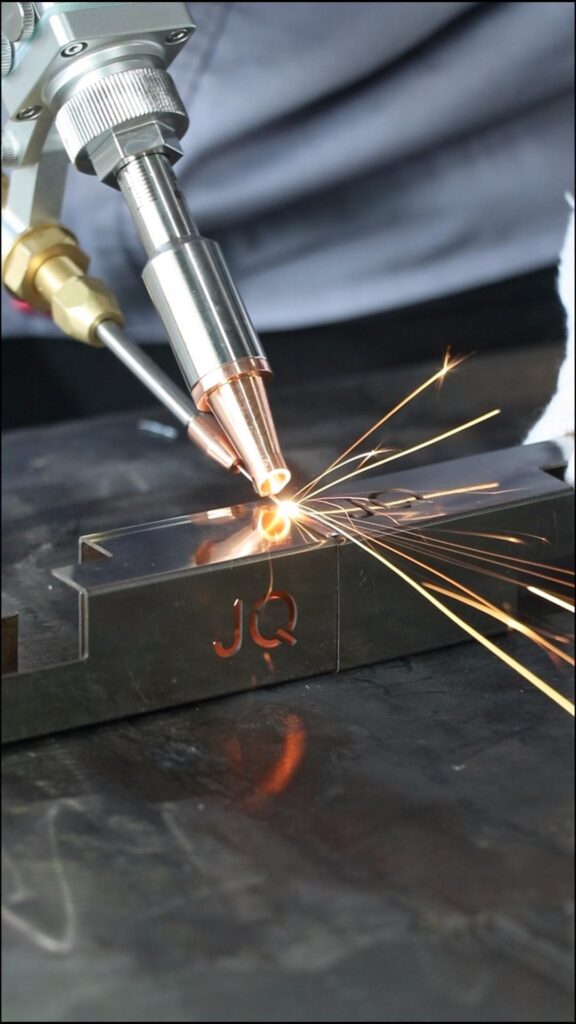
1.2 Characteristics of laser welding technology
Through the continuous exploration and innovation of researchers, laser welding technology has been successfully developed and widely used. In some areas, laser welding technology has completely replaced traditional welding technology. This is due to the unique advantages of laser welding technology. First of all, the heat-affected zone of laser welding technology is relatively small, because the laser beam directly irradiates the welding part and will not have a negative impact on other areas. Secondly, the laser beam concentration of laser welding technology can generate high heat, thereby improving welding efficiency and ensuring the overall quality of welded parts. Finally, laser welding technology can weld hidden and hard-to-reach parts. With its flexibility, it can be achieved by reasonably controlling the direction of the laser beam .
2 Application advantages and disadvantages of laser welding technology
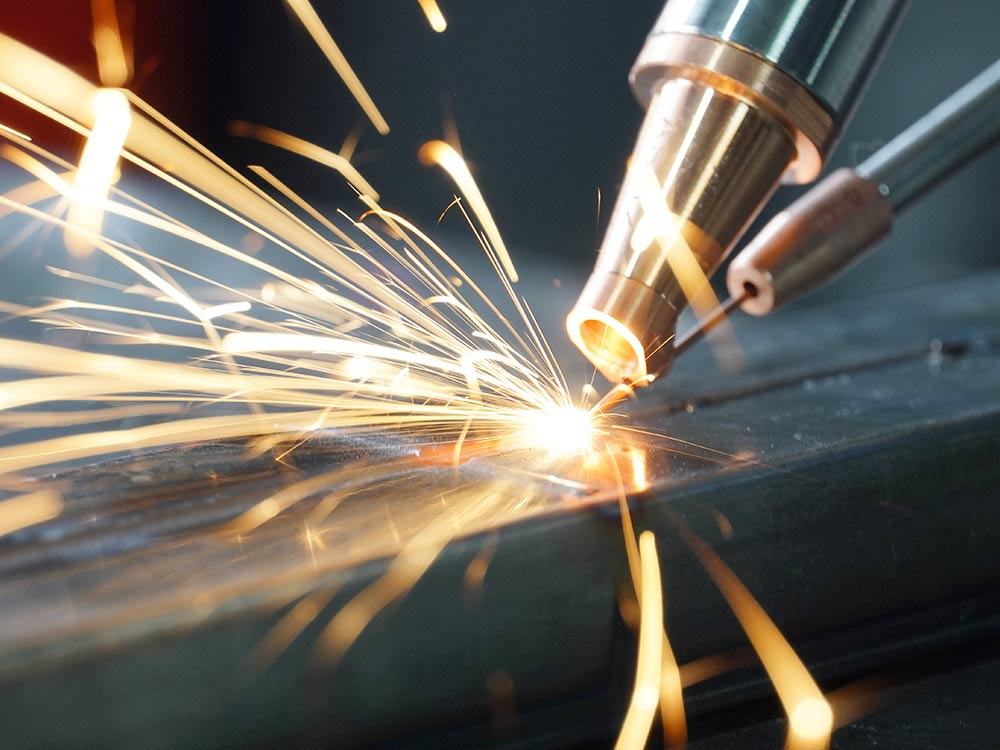
2.1 Application advantages of laser welding technology In modern industrial production and processing, laser welding technology is very popular, which is mainly due to the obvious advantages of laser welding technology compared with traditional methods. It is mainly reflected in the following aspects. First, compared with traditional welding technology, the structural strength and aspect ratio of laser welding are higher, the welding quality is better, and the welding speed is faster; second, compared with traditional welding technology, Compared with laser welding, it has lower environmental requirements. Welding operations can be performed in a vacuum environment, and remote automated operations can be achieved with the help of optical fibers and lenses. Thirdly, compared with traditional welding technology, the density of laser energy is relatively greater. The power is relatively higher, and it can effectively weld materials that are relatively difficult to weld, such as quartz and titanium, and is applicable to a wider range of materials.
2.2 At the same time, we should also pay attention to the application shortcomings of laser welding technology. Although laser welding technology has many advantages, it inevitably also has some shortcomings, which are mainly reflected in the following aspects. First, compared with traditional welding technology, the prices of lasers and other welding accessories involved in laser welding are relatively high, and the investment in early equipment and the maintenance of later equipment require a large cost, which to a certain extent also makes The economic benefits cannot be maximized; secondly, compared with traditional welding technology, the laser absorption rate of solid materials in laser welding is relatively low. When plasma materials appear, the conversion effect of laser welding will be greatly reduced to a certain extent. ; Thirdly, compared with traditional welding technology, the laser focal length spot in laser welding is relatively small, which means that the accuracy of the equipment is required to be higher. Even a small error may cause It causes great deviations in the overall processing.
3 Mode quality characteristics of laser welding
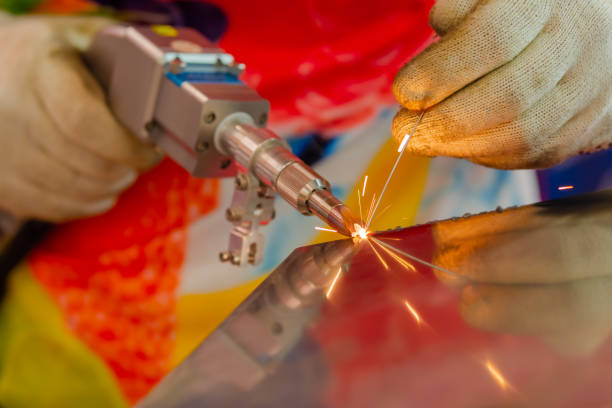
3.1 Thermal conduction welding
Thermal conduction welding refers to irradiating the surface of the material with laser, reflecting and absorbing part of the laser, converting light energy into heat energy, heat melting the surface of the material, and transferring the heat energy to the depth of the material through thermal conduction. , and finally realize the welding of the weldment.
3.2 Laser deep penetration welding
The so-called laser deep penetration welding means that under the irradiation of a laser beam with a high power density, the light energy is absorbed by the material and converted into heat energy. When the material is heated to the vaporization temperature, a large amount of metal vapor will be produced, and a reaction force will be generated when the vapor is pushed out of the material surface. This reaction force forces the molten metal to move around, forming pits. As the laser continues to illuminate, the pits become deeper. When the laser irradiation stops, the liquid around the pit will flow back. After cooling, the two weldments are welded together .
3.3 Quality characteristics of heat conduction welding and laser deep penetration welding According to the actual material properties and welding requirements, the heat conduction welding and laser deep penetration welding mechanisms are selected, and different welding mechanisms are achieved by adjusting various laser welding process parameters. The biggest difference between heat conduction welding and laser deep penetration welding is that the surface of the heat conduction welding molten pool remains closed, while the laser deep penetration welding molten pool will be penetrated into holes by the laser beam. In heat conduction welding, since the laser beam is difficult to penetrate the material to be welded, the disturbance to the system is relatively small, and the weld is not easily invaded by gas. However, during laser deep penetration welding, pores may occur due to the continuous closing of small holes. Additionally, thermal conduction welding and laser deep penetration welding can be interchanged within the same welding process, depending on the peak laser energy density and laser pulse duration applied to the workpiece.
3.4 Laser welding is an efficient and precise welding method that improves the structural properties of laser welding seams and is widely used in aerospace, automobile manufacturing, electronic equipment and other fields. The structural properties of laser welding seams play an important role in the quality of welded joints. The structural properties of laser welding seams determine the strength of the welded joint. During the laser welding process, under the action of the high energy density of the laser beam, the welded joint is instantly heated and rapidly cooled, and the metal grains in the weld area rapidly grow and rearrange. This rapid cooling results in smaller and elongated grain sizes in the weld area, creating a dense lattice structure. Due to the fine grain size, the grain boundary strength is relatively high, thereby improving the strength of the welded joint. The structural properties of laser welded seams are crucial to the corrosion resistance of the joint. Due to the rapid cooling rate of laser welding, the metal grains in the weld area are rearranged to form a dense lattice structure, reducing the generation of pores and inclusions. This organizational structure can effectively prevent corrosion from corrosive media and improve the corrosion resistance of welded joints.
4 Application fields of laser welding technology
4.1 Manufacturing applications
Laser welding technology has high welding speed and precision. The heat source of the laser beam heats the workpiece in a very short time, allowing for a fast welding process. Moreover, the diameter of the laser beam can be adjusted to precisely control the position and shape of the welding, ensuring the accuracy and stability of the welded joint. Laser welding technology can also be applied to the welding of various materials. Whether metal, plastic or ceramic, laser welding can effectively join. This makes laser welding widely used in the manufacturing processes of different industries, such as automobile manufacturing, electronic equipment manufacturing, shipbuilding, etc. Laser welding technology is not only used in traditional manufacturing, but also plays a role in the emerging advanced manufacturing field. important role. For example, 3D printing technology combined with laser welding can realize customized manufacturing of complex structures, bringing many innovation and development opportunities to the manufacturing industry.
4.2 Laser welding technology
Application in the field of powder metallurgy The introduction of technology has brought new opportunities and challenges to the application of powder metallurgy materials. Laser welding is unique in its high energy density and instantaneity, allowing it to achieve high-quality connections and welds in the manufacturing process of powder metallurgy materials. Compared with traditional welding methods, laser welding has a smaller heat-affected zone, higher welding speed and more precise welding control, thereby improving welding strength and high temperature resistance.
4.3 Application in electronic industry
Laser welding has been widely used in the electronic industry, especially in the microelectronics industry. With its high precision, high efficiency and non-contact characteristics, it has become an indispensable key technology in the manufacturing process of microelectronic devices. The application of laser welding in the microelectronics industry is mainly concentrated in the manufacturing process of microchips and electronic components. Microchips are the core of modern electronic products, and their manufacturing process requires precise and stable welding technology. Laser welding meets the high demands of microchips with its small weld seams, high welding speeds and precise welding control. In addition, laser welding can also be used to connect electronic components, such as welding on electronic circuit boards, which can achieve high-density component layout and improve the overall performance of electronic devices. The application of laser welding in the microelectronics industry also involves the processing of microstructures. Microelectronic devices often require the processing of microstructures and the connection of nanomaterials, which requires high-precision processing technology. Laser welding can achieve micro-sized welding and cutting by adjusting the laser power and focal length to meet the microstructure processing needs of microelectronic devices.
4.4 Biomedical applications
With the successful application of laser welding technology in the biomedical field, its potential in surgery and tissue repair has gradually been revealed. In current research, laser welding technology has been applied to the repair of more complex biological structures, such as human fallopian tubes and blood vessels. These experimental results show that laser welding not only has a fast anastomosis speed, but also does not produce foreign body reactions during the healing process, which provides valuable reference value for further development in the biomedical field.
4.5 Application in the air-conditioning and refrigeration industry
At present, our laser welding technology is mainly used in the welding of liquid distributor parts on falling film evaporators and the welding of air-conditioning sheet metal parts (such as panels, side panels, top and bottom plates, etc.). In order to ensure that the air-conditioning Regarding the cleanliness of the internal parts of the condenser and evaporator after welding, our company is currently studying the use of high-power dual-wire laser welding technology and has made certain progress.
5 Development Trend of Laser Welding Technology
5.1 At the current stage of hybrid welding, the plasma cloud existing in laser welding has the effect of absorbing and reflecting laser, which to a certain extent also greatly weakens the absorption of laser by metal materials, resulting in laser damage. It is difficult to fully utilize the energy. At the same time, the requirements for the interface part of the welding base metal must also be increased during the welding process, so as to avoid the occurrence of misalignment and pores as much as possible, thereby minimizing the phenomenon of looseness and cracks in the welded part. In addition, the interface part after laser welding will be dented. Therefore, in order to better reduce the shortcomings of single-heat source laser welding, more heat sources with heating characteristics should be introduced while maintaining the current advantages to form Hybrid heat source welding, thereby promoting the future development of welding technology.
5.2 Laser welding control
Laser power control is one of the most basic control parameters in laser welding. The size of the laser power directly affects the formation and stability of the molten pool during the welding process. By adjusting the laser power, the temperature and melting depth of the molten pool can be controlled, thereby controlling the welding quality. Welding speed control is another important control parameter. The speed of welding directly affects the formation of the weld and the stability of the molten pool. If the welding speed is too fast, the weld may be incomplete or the molten pool may be unstable; if the welding speed is too slow, the molten pool may be too large or weld defects may occur during the welding process. Therefore, it is crucial to select the appropriate welding speed based on specific welding requirements and material properties. Weld seam tracking control is a control method for complex welding structures. In some complex welding scenarios, the welding path may have curves, angle changes, etc., so welding seam tracking control is required to ensure welding quality. Welding seam tracking control mainly relies on laser welding robots or other automated welding equipment to ensure the precise position and shape of laser welding seams by tracking and adjusting the welding seam path.
6 Conclusion
Based on the above discussion, this article conducts a simple analysis of the overview of laser welding technology, mode quality characteristics, application advantages, advantages and disadvantages, application fields and development trends. It can be seen that laser technology is widely used in various industries. By strengthening the research on laser welding technology, we will find, discover and solve its own defects and deficiencies, and continuously improve production work, thereby promoting the application and development of laser welding technology.